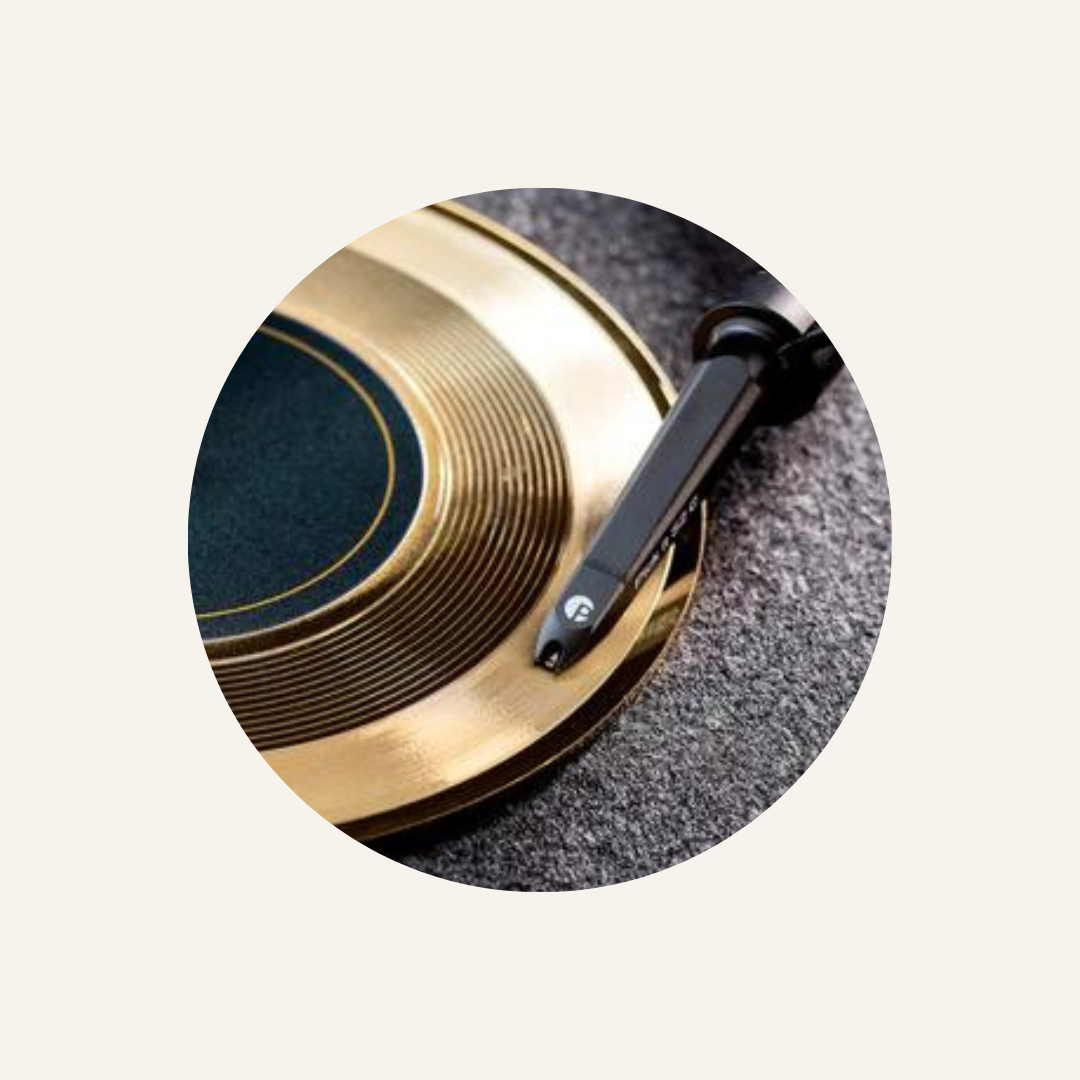
Inside the Grooves of Precious Sound Records
There is magic behind the music that plays, but what is even more magical is the science behind how the music plays. On today’s edition of The Frequency, we get down to the bottom of how our Precious Sound records provide that clear and robust audio we all know and love.
Before we get to the inner workings of our precious metal records and the technology that is used to craft them, we must discuss the basics of records and how they were created.
French inventor Édouard-Léon Scott de Martinville built the first known sound recording machine in the early 1800s. What he called the phonautograph visually recorded vibrations of sounds, which became a key player in the creation of many other musical machines down the line, like Thomas Edison’s phonograph in 1877. In 20 short years, the phonograph had been improved by inventors like Alexander Graham-Bell, and German-American inventor Emile Berliner who patented the first sound recording device coined the gramophone.
One of Berliner's earliest disks.
It utilized grooved, flat disks, rather than cylinders, and these disks became known as the first records that were later made out of vinyl. It wasn't long before companies jumped on Berliner's design, and by the 1900s, mass-market gramophones were ready for the public. These were brought into homes and public places, and are the disc-shaped records we know and love today.
A question that often escapes us is HOW does the music transmit from these vinyl discs to our ears so warmly? Vinyl records work by capturing sound waves through a recording process and storing them on the record. These sound waves are then translated into physical grooves on the record. The groove is surprisingly V-shaped, and each side of the groove “wall” carries one of the stereo signals. The right channel is carried by the side closest to the outside of the record, and the left is carried by the inside wall. The frequency and amplitude (volume) information are a reflection of the groove’s width and depth. If there’s too much bass, a needle could quite literally jump out of the groove! It’s the job of the mastering engineer to get it just right when doing the vinyl transfer.
A close up image of the intricate groove detail on our records.
Next, the stylus, made from a diamond or other hard material, reads the grooves as the turntables, the circular plate that the record sits on spins the record. As the needle moves through the grooves, it transmits the vibrations along a flexible metal strip and wiring in the cartridge at the end of the tone arms, creating an electrical signal that is sent to an amplifier. The amplifier boosts the signal, which is then sent to the speakers, producing the sound we hear.
The core of the technology is very simple, but the details can deeply impact the experience which is why at Precious Sound, we have used the renowned modern technology to provide the best sound for our customers. We utilize Direct Metal Mastering, or DMM for short. It eliminates three complicated steps from the production process because the copper master can be directly galvanized and turned into the stamper that presses the vinyl records.
Precious Sound's DMM machine and the copper master.
The use of lacquer masters requires more production steps that involve dangerous chemicals and is prone to introduce production errors through the added complexity. This not only makes DMM more environmentally friendly, but it also enables a more reliable and streamlined production. Most importantly, it has many tonal benefits as well.
From a sound perspective, DMM delivers a technically superior product. It eliminates pre- and post-echo, a problem that has plagued vinyl records since their inception. It results from the cutter head accidentally transferring some of the signal to the previously cut groove, which is due to the relative softness of lacquer. The high frequencies are crisp and present in DMM cuts, and the depth and clarity are phenomenal. Stereo imaging is enhanced, and the noise floor is significantly reduced. A modern DMM cut is the clearest high-fidelity listening experience available on vinyl today.
The sound is particularly wide and clear on our precious metal records. And Ludwig, our master engineer, likes to point out his favorite feature: the stereo field being very stable and wide, making the music sound much more natural to our ears. Early records only had a single channel until the first stereo records were released in the late 50s. When reading a mono record, the stylus only moves horizontally, while the needle moves both horizontally and vertically on a stereo record.
The two channels are created by encoding the music at a 90-degree angle with each channel on one side of the groove. This is achieved by engineering each groove at a 45-degree angle from the top of the record. See the diagram for a visualization of a stereo groove.
Our Precious Sound record.
We use precious metals to craft our playable records, and these metals are 8x harder than vinyl. Have no fear, although our records are much tougher than vinyl, your diamond stylus is still harder than the record. To avoid scratching, our records include a generous lead-in and lead-out groove, so you can avoid scratching the record's grooves when placing or lifting the needle.
We take so much pride in our modern approach to this incredible science. These records are not only thoroughly enjoyed by all who listen, but they serve as keepsakes and future heirlooms that may live on forever.